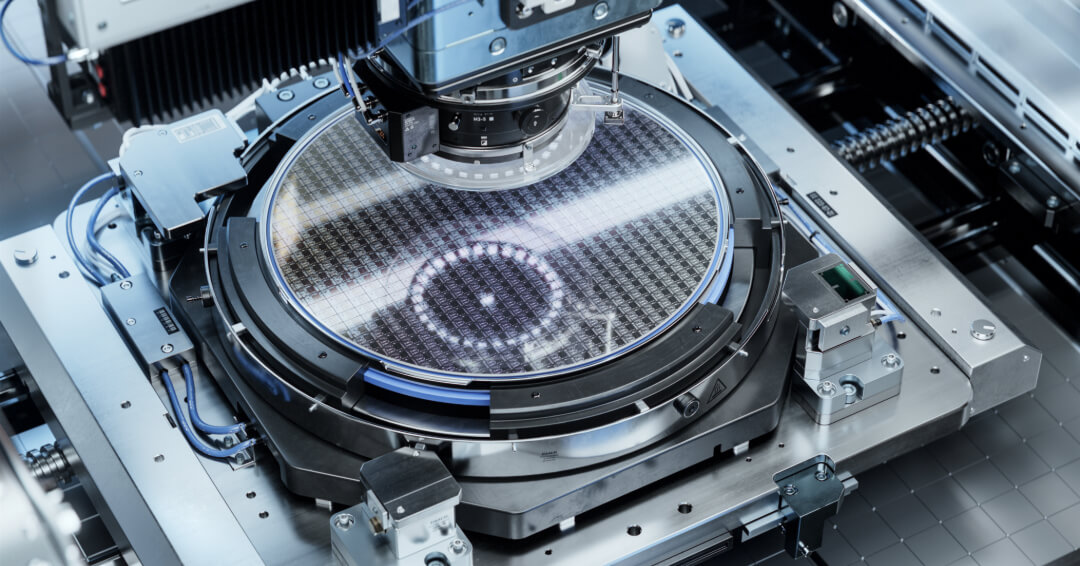
Overview of Semiconductor Manufacturing
Semiconductor manufacturing is a complex process that involves multiple steps to create integrated circuits (ICs) on silicon wafers. These ICs are the building blocks of modern electronics, powering everything from smartphones to supercomputers. One of the most critical steps in this process is lithography, which involves patterning the intricate designs of electronic circuits onto the wafer. The ability to create smaller and more precise patterns has been the driving force behind the exponential growth of computing power, following Moore's Law, which predicts the doubling of transistor density on ICs approximately every two years.
Importance of Lithography
Lithography is pivotal because it defines the minimum feature size and, consequently, the density of transistors on a chip. As transistors become smaller, more can fit onto a single chip, increasing its performance and reducing power consumption. This miniaturization has fueled the advancement of technology, enabling the creation of more powerful and efficient electronic devices.
Historical Context
The journey of lithography began in the 1950s with the use of visible light to transfer patterns onto photoresist-coated wafers. Over the decades, lithography has evolved through various technological paradigms, each marked by significant advancements in resolution and precision. This article will explore the evolution of lithography, from its early days to the current state-of-the-art Extreme Ultraviolet (EUV) lithography and beyond.
Beginnings of Lithography
The origins of lithography in semiconductor manufacturing can be traced back to the 1950s, when the semiconductor industry was in its infancy. The first lithographic techniques utilized visible light to project patterns from a photomask onto a photosensitive material called photoresist, which was coated onto the silicon wafer. These early methods were relatively crude, with feature sizes in the micrometer range.
Transition to Ultraviolet Lithography
As the demand for higher performance and smaller devices grew, the limitations of visible light lithography became apparent. In the 1970s and 1980s, the industry transitioned to using ultraviolet (UV) light, which has a shorter wavelength and thus can create smaller features. This shift marked the beginning of significant improvements in lithographic resolution
Basics of Optical Lithography
Optical lithography, particularly using deep ultraviolet (DUV) light, has been the mainstay of semiconductor manufacturing for several decades. The technique involves projecting light through a photomask to create a pattern on a photoresist layer. The resolution of optical lithography is limited by the wavelength of light used, with shorter wavelengths enabling finer features.
The Diffraction Limit
As feature sizes approached the wavelength of light used, diffraction effects became a limiting factor. Diffraction causes light to spread out when it passes through small openings, making it difficult to create sharp patterns at sub-wavelength scales.
Techniques to Overcome Diffraction Limits
1. Immersion Lithography: Introduced in the mid-2000s, immersion lithography involves placing a liquid medium (typically water) between the lens and the wafer to increase the numerical aperture and improve resolution. The higher refractive index of the liquid allows for better focusing of the light, enabling smaller features.
Sugerencia de imagen: Diagrama que explique el proceso de litografía por inmersión, mostrando el medio líquido entre la lente y la oblea.
2. Phase-Shift Masks: Phase-shift masks (PSMs) enhance resolution by modifying the phase of the light passing through the mask. This technique uses interference patterns to sharpen the edges of the features.
Sugerencia de imagen: Ilustración de máscaras de cambio de fase y cómo modifican las fases de la luz para mejorar la nitidez del patrón.
3. Optical Proximity Correction (OPC): OPC involves adjusting the shapes on the mask to counteract the distortions caused by diffraction. This technique uses computational methods to predict and correct these distortions.
Sugerencia de imagen: Ejemplo de una fotomáscara antes y después de la corrección de proximidad óptica, mostrando los ajustes realizados en los patrones de la máscara.
Deep Ultraviolet (DUV) Lithography
Deep ultraviolet (DUV) lithography, using 193 nm wavelength light, has been the dominant technology for semiconductor manufacturing for many years. DUV lithography has enabled the production of features as small as 20 nm, pushing the limits of optical resolution.
Tools and Equipment Advancements
The development of advanced lithographic tools and equipment has been crucial in achieving these fine features. High numerical aperture (NA) lenses, advanced photoresists, and precision alignment systems have all contributed to the success of DUV lithography.
Computational Lithography
Computational lithography encompasses various techniques that use computer algorithms to optimize the lithographic process. This includes OPC, model-based synthesis, and source mask optimization (SMO), which together help to mitigate the effects of diffraction and other distortions.
Sugerencia de imagen: Diagrama de flujo de las técnicas de litografía computacional, destacando OPC, SMO y síntesis basada en modelos.
Definition and Significance of EUV Lithography
Extreme Ultraviolet (EUV) lithography represents one of the most significant advancements in semiconductor manufacturing. EUV lithography uses light with a wavelength of 13.5 nm, which is much shorter than the DUV wavelengths, allowing for much smaller feature sizes and higher transistor densities.
Technical Challenges and Solutions.
The path to EUV implementation has been fraught with technical challenges, particularly in generating and managing EUV light. EUV lithography requires extremely high-energy light sources and complex optical systems to achieve the desired resolution. The main challenges and their solutions are mentioned below:
1. EUV Light Sources: Generating EUV light involves creating a plasma that emits at the desired wavelength. The two main methods are laser-produced plasma (LPP) and discharge-produced plasma (DPP). LPP uses high-power lasers to vaporize a target material, while DPP uses electrical discharges to create plasma.
Sugerencia de imagen: Diagrama de una fuente de luz EUV, mostrando la generación de plasma y la emisión de luz EUV.
2. Optical Systems: Traditional optical materials are not suitable for EUV wavelengths, so EUV lithography uses multilayer mirrors to reflect and focus the light. These mirrors are made by depositing alternating layers of materials with different refractive indices, creating a structure that can efficiently reflect EUV light.
Sugerencia de imagen: Vista en sección transversal de un espejo multicapa utilizado en la litografía EUV.
3. Mask Technology: EUV masks, or reticles, are also different from traditional masks. They are made with a reflective surface and must be free of defects to ensure high-quality patterning. Mask inspection and defect repair are critical processes in EUV lithography.
Sugerencia de imagen: Imagen detallada de una máscara EUV, destacando la superficie reflectante y las características del patrón.
Development of EUV Photoresists
Developing photoresists that are sensitive to EUV light has been a crucial area of research. EUV photoresists must balance sensitivity, resolution, and line-edge roughness to produce high-quality patterns. Chemical amplification mechanisms are often used to enhance the sensitivity of these photoresists.
Post-Exposure Processing
The post-exposure processing steps are equally critical in EUV lithography. These steps involve the development of the exposed photoresist, followed by etching processes to transfer the pattern onto the underlying material. Precise control of these processes is essential to maintain pattern fidelity and avoid defects.
Technical and Economic Barriers
The adoption of EUV lithography in the semiconductor industry has been a gradual process, driven by both technical advancements and economic considerations. EUV systems are expensive, and the initial costs of implementation are high. However, the long-term benefits of higher resolution and greater transistor densities make EUV lithography an attractive investment for leading semiconductor manufacturers.
Case Studies of EUV Implementation
Leading manufacturers such as TSMC, Intel, and Samsung have invested heavily in EUV technology. These companies have successfully integrated EUV lithography into their production lines, overcoming initial hurdles related to throughput, defectivity, and tool uptime.
Current State and Future Prospects
EUV lithography is now being used in the production of advanced nodes, such as 7 nm, 5 nm, and below. The technology continues to evolve, with ongoing research focused on improving source power, mask quality, and resist performance. The future of EUV looks promising, with potential applications in even more advanced semiconductor nodes.
Sugerencia de imagen: Línea de tiempo que muestre la adopción de la litografía EUV por los principales fabricantes de semiconductores, destacando hitos y avances clave.
X-ray Lithography
X-ray lithography uses even shorter wavelengths than EUV, allowing for extremely fine features. However, it faces challenges such as high costs and the need for new materials and processes. Despite these hurdles, X-ray lithography holds promise for future semiconductor manufacturing.
Electron Beam Lithography
Electron beam lithography (e-beam) offers high resolution and precision, making it ideal for research and development applications. However, its low throughput makes it less suitable for mass production. Advances in multi-beam systems aim to address this limitation and make e-beam lithography more viable for commercial use.
Focused Ion Beam Lithography
Focused ion beam (FIB) lithography uses a beam of ions to directly write patterns onto a substrate. This technique offers high resolution and flexibility but is slow and expensive. FIB is often used for prototyping and repairing masks and other critical components.
Nanoimprint Lithography
Nanoimprint lithography (NIL) physically stamps patterns onto substrates using molds. NIL is cost-effective and capable of producing high-resolution patterns, making it suitable for certain applications. However, it faces challenges in achieving uniformity and scalability.
Sugerencia de imagen: Tabla comparativa de diferentes técnicas litográficas emergentes, destacando sus ventajas y desafíos.
New Photoresist Materials
Innovations in photoresist materials are essential for advancing lithography. Researchers are developing new resists that offer higher sensitivity, better resolution, and improved line-edge roughness. These materials must also be compatible with existing processes and equipment.
Nanomaterials in Lithography
Nanomaterials, such as carbon nanotubes and graphene, are being explored for their potential applications in lithography. These materials offer unique electrical, thermal, and mechanical properties that could enable new lithographic techniques and improve existing ones.
Advanced Substrates and Coatings
Advanced substrates and coatings play a crucial role in lithographic processes. These materials must provide a stable and uniform surface for patterning while being compatible with the various chemicals and processes used in lithography.
Sugerencia de imagen: Modelo molecular de un nuevo material fotoresistente e imágenes de nanomateriales utilizados en la investigación litográfica.
Hybrid Lithography Systems
Hybrid lithography systems combine multiple lithographic techniques to achieve higher resolution and throughput. For example, a system might use both EUV and electron beam lithography to optimize the patterning process. These hybrid systems aim to leverage the strengths of each technique while mitigating their weaknesses.
High-NA EUV Lithography
High-numerical-aperture (NA) EUV lithography is an extension of traditional EUV that uses lenses with higher NA to achieve better resolution. This approach requires significant advancements in optics and materials but holds the potential to further push the boundaries of lithographic resolution.
Multi-Beam and Maskless Lithography
Multi-beam and maskless lithography systems use arrays of beams to directly write patterns onto substrates without the need for masks. These systems offer high precision and flexibility, making them suitable for prototyping and low-volume production. Advances in beam control and alignment are essential for their success.
Sugerencia de imagen: Diagrama de un sistema de litografía EUV de alta NA y una configuración de litografía multihaz sin máscara, destacando sus características y capacidades únicas.
Cost Analysis and Economic Considerations
The evolution of lithography has profound economic implications for the semiconductor industry. The development and implementation of new lithographic techniques require significant investment in research, equipment, and materials. However, the benefits in terms of increased performance, reduced power consumption, and higher transistor densities can outweigh these costs.
Technological Advancements Driven by Lithography
Advancements in lithography have driven numerous technological breakthroughs in the semiconductor industry. These include the development of high-performance processors, memory devices, and sensors that power modern electronics. Lithography has also enabled the miniaturization of devices, leading to more compact and efficient electronic products.
Competitive Landscape in the Semiconductor Industry
The competitive landscape of the semiconductor industry is heavily influenced by advancements in lithography. Companies that invest in cutting-edge lithographic techniques can gain a significant advantage in terms of performance, cost, and time-to-market. As a result, leading semiconductor manufacturers continually strive to stay at the forefront of lithographic innovation.
Sugerencia de imagen: Gráfico de análisis económico de los costos versus beneficios de la litografía, destacando el impacto a largo plazo en la industria de los semiconductores.
Case Studies of Leading Semiconductor Manufacturers
Detailed case studies of leading semiconductor manufacturers such as TSMC, Intel, and Samsung highlight the practical applications and benefits of advanced lithographic techniques. These case studies showcase how these companies leverage lithography to innovate and stay competitive in the market.
1. TSMC: Has been a pioneer in adopting EUV lithography, using it to produce cutting-edge nodes such as 7 nm and 5 nm. Their success with EUV has enabled them to maintain a leadership position in the foundry market.
Sugerencia de imagen: Línea de tiempo de la adopción de la litografía EUV por parte de TSMC, destacando hitos y avances clave.
2. Intel: Has invested heavily in developing advanced lithographic techniques, including high-NA EUV. Their focus on pushing the boundaries of lithography has driven innovations in their processors and other semiconductor products.
Sugerencia de imagen: Ilustración de las innovaciones litográficas de Intel y su impacto en el rendimiento de los procesadores.
3. Samsung: Has integrated EUV lithography into its production lines for memory and logic devices. Their efforts have resulted in significant advancements in performance and efficiency for their semiconductor products.
Sugerencia de imagen: Estudio de caso sobre el uso de la litografía EUV por parte de Samsung en la producción de dispositivos de memoria, mostrando los beneficios logrados.
Applications in Consumer Electronics and Industrial Uses
The advancements in lithography have far-reaching implications beyond semiconductor manufacturing. High-resolution lithographic techniques enable the production of compact and powerful consumer electronics such as smartphones, tablets, and laptops. In industrial applications, advanced lithography supports the development of high-performance sensors, communication devices, and other critical technologies.
Summary of Key Points
The evolution of lithography has been a driving force behind the exponential growth of semiconductor technology. From the early days of visible light lithography to the current state-of-the-art EUV systems, each advancement has enabled significant strides in performance, efficiency, and miniaturization.
Future Outlook and Ongoing Research
The future of lithography holds promise for even more groundbreaking developments. Ongoing research into high-NA EUV, multi-beam systems, and new materials will continue to push the boundaries of what is possible in semiconductor manufacturing. As technology evolves, lithography will remain a critical enabler of innovation and progress.
Final Thoughts on the Significance of Lithography
Lithography is not just a manufacturing technique; it is the cornerstone of the semiconductor industry. Its evolution reflects the relentless pursuit of precision, efficiency, and miniaturization that drives technological advancement. As we look to the future, lithography will continue to play a pivotal role in shaping the electronic landscape and enabling the next generation of innovations.